Comprehending the Basics and Applications of Plastic Extrusion in Modern Production
In the realm of contemporary manufacturing, the strategy of plastic extrusion plays an important role. Unraveling the basics of this procedure reveals the real adaptability and potential of plastic extrusion.
The Basics of Plastic Extrusion Refine
While it may show up complicated, the fundamentals of the plastic extrusion process are based on fairly straightforward principles. It is a manufacturing procedure wherein plastic is thawed and afterwards shaped right into a constant profile with a die. The raw plastic material, typically in the form of pellets, is fed into an extruder. Inside the extruder, the plastic is subjected to heat and pressure, triggering it to thaw. The liquified plastic is after that required via a shaped opening, known as a die, to form a long, constant item. The extruded item is cooled down and after that cut to the desired size. The plastic extrusion process is thoroughly made use of in numerous industries as a result of its cost-effectiveness, versatility, and efficiency.
Various Sorts Of Plastic Extrusion Methods
Structure upon the fundamental understanding of the plastic extrusion procedure, it is necessary to discover the different strategies involved in this production approach. The two key techniques are profile extrusion and sheet extrusion. In account extrusion, plastic is thawed and developed into a continual account, usually used to create pipelines, poles, rails, and window structures. In contrast, sheet extrusion produces huge, level sheets of plastic, which are typically further processed into items such as food product packaging, shower drapes, and car components. Each strategy needs specialized machinery and accurate control over temperature level and pressure to make certain the plastic preserves its form throughout cooling. Understanding these techniques is crucial to making use of plastic extrusion efficiently in modern-day manufacturing.

The Duty of Plastic Extrusion in the Automotive Market
An overwhelming majority of components in modern-day automobiles are products of the plastic extrusion process. This process has actually reinvented the automobile market, transforming it right into a much more effective, cost-efficient, and versatile production market. Plastic extrusion is mainly used in the production of various auto elements such as bumpers, grills, door panels, and dashboard trim. The procedure offers an attire, consistent output, making it possible for manufacturers to create high-volume get rid of terrific precision and marginal waste. The lightness of the extruded plastic parts contributes to the total reduction in car weight, enhancing fuel efficiency. The durability and resistance of these components to warmth, cool, and impact enhance the longevity of autos. Thus, plastic extrusion plays an essential function in vehicle production.

Applications of Plastic Extrusion in Customer Goods Manufacturing
Past its substantial impact on the automobile industry, plastic extrusion verifies equally reliable in the realm of durable goods making. This process is crucial in producing a large selection of items, from food packaging to family appliances, toys, and even clinical tools. The flexibility of plastic extrusion enables browse this site makers to create and produce complicated sizes and shapes with high accuracy and efficiency. Due to the recyclability of lots of plastics, squeezed out elements can be reprocessed, lowering waste and cost (plastic extrusion). The adaptability, adaptability, and cost-effectiveness of plastic extrusion make it a favored choice for numerous customer goods makers, contributing substantially to the market's development and innovation. Nevertheless, the her comment is here environmental implications of this prevalent use need careful factor to consider, a topic to be reviewed additionally in the subsequent section.
Environmental Impact and Sustainability in Plastic Extrusion
The pervasive usage of plastic extrusion in manufacturing welcomes analysis of its eco-friendly effects. As a procedure that often utilizes non-biodegradable materials, the ecological impact can be substantial. Energy consumption, waste production, and carbon exhausts are all problems. Nevertheless, industry innovations are enhancing sustainability. Efficient machinery minimizes power use, while waste administration systems recycle scrap plastic, reducing resources needs. Additionally, the advancement of eco-friendly plastics uses a more environmentally friendly option. Despite these renovations, further advancement is needed to mitigate the environmental impact of plastic extrusion. As society leans towards sustainability, suppliers must adjust to stay sensible, stressing the significance of constant research study and improvement in this field.
Final thought
Finally, plastic extrusion plays a critical function in modern manufacturing, particularly in the automotive and consumer goods fields. Its flexibility permits the advice manufacturing of a wide variety of components with high accuracy. In addition, its capacity for reusing and advancement of eco-friendly products uses an encouraging method in the direction of sustainable methods, therefore dealing with environmental worries. Comprehending the fundamentals of this process is key to optimizing its advantages and applications.
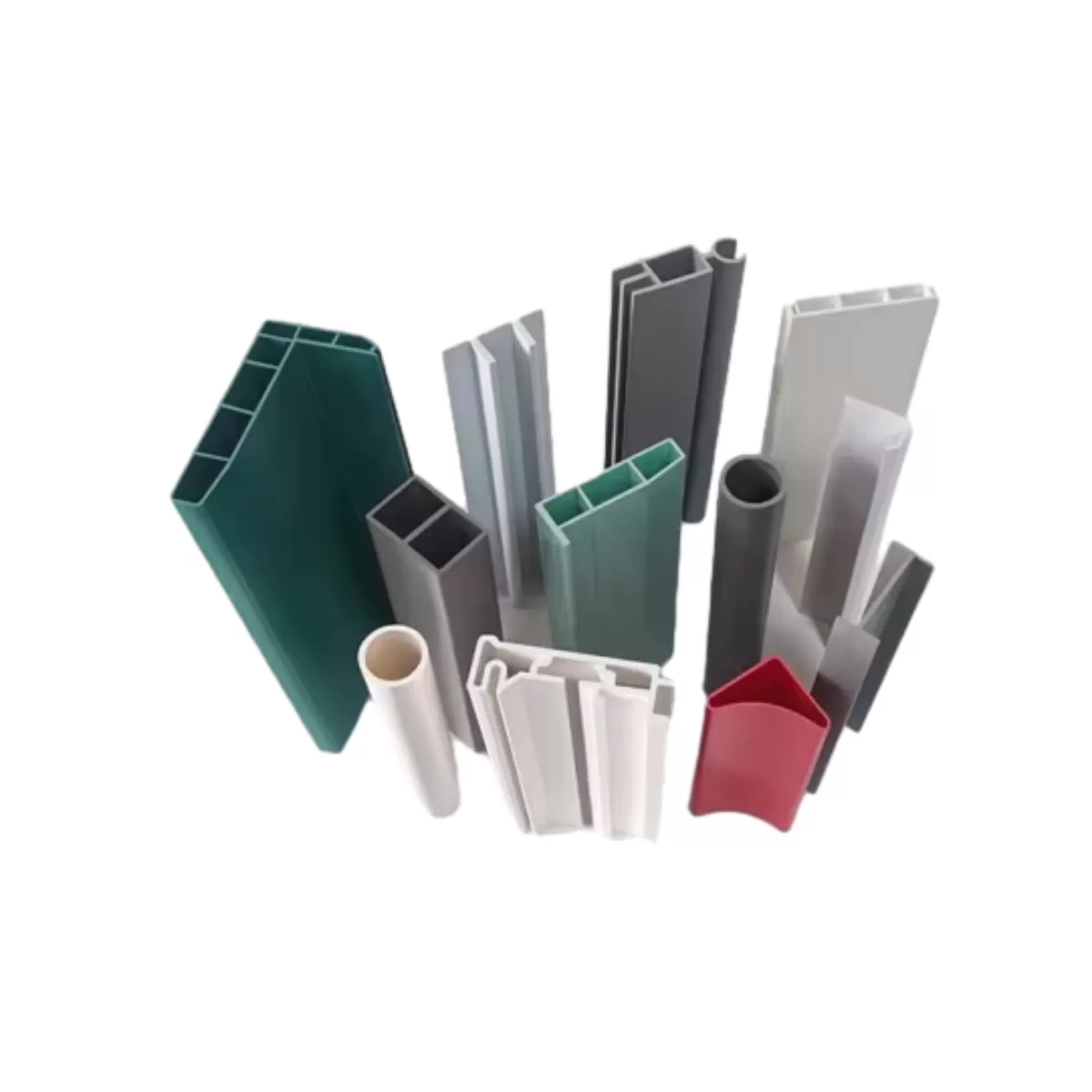
The plastic extrusion process is extensively used in various industries due to its cost-effectiveness, adaptability, and efficiency.
Building upon the basic understanding of the plastic extrusion procedure, it is required to discover the different methods included in this production approach. plastic extrusion. In contrast, sheet extrusion develops large, flat sheets of plastic, which are generally additional refined into items such as food product packaging, shower curtains, and car parts.A frustrating majority of parts in contemporary automobiles are products of the plastic extrusion process